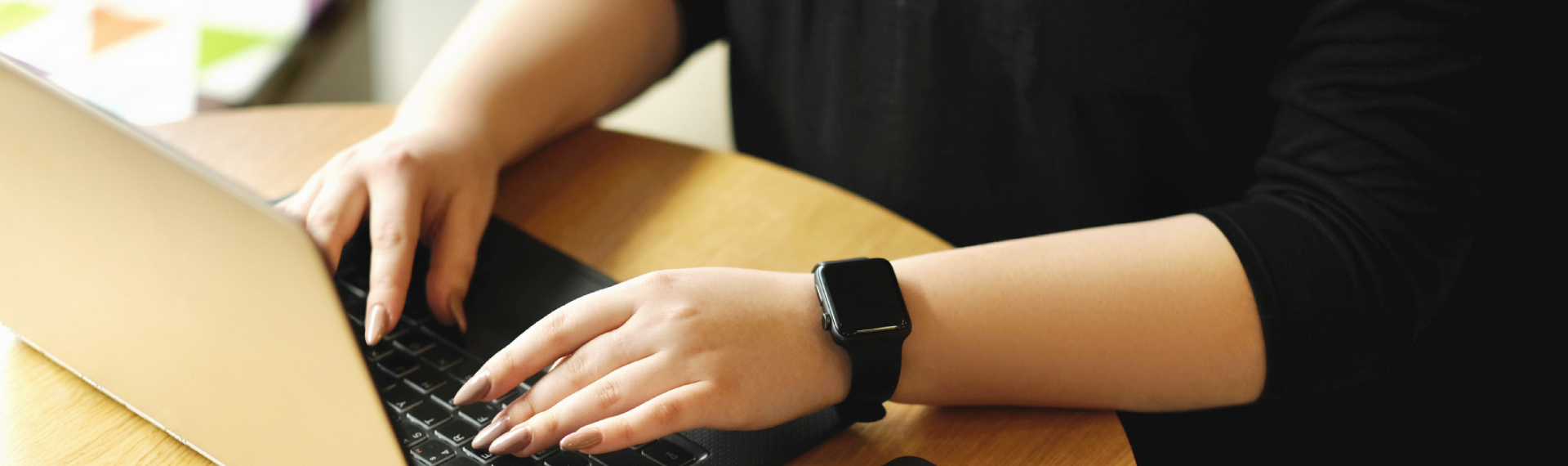
Lift Manufacturing Process: Excellence in Quality, Safety and Engineering
Lift systems have become an indispensable part of high-rise buildings, directly influencing the comfort and functionality of modern living spaces. Behind every reliable lift lies advanced engineering, meticulous production processes, and an uncompromising commitment to quality.
At Ametal, we combine safety, quality, and cutting-edge technology to deliver products that exceed customer expectations. Every component we produce is developed and manufactured in line with international standards, from the initial design to final quality control. So, how does a lift come to life? Let’s explore the key stages of the lift manufacturing process.
- Needs Assessment & Project Planning
Every project begins with a detailed analysis tailored to the specific building. Factors such as the number of floors, building type (residential, commercial, hospital, etc.), passenger flow, and architectural layout are evaluated. Based on this, our engineering team prepares technical designs and system plans compliant with global standards.
- Design & Engineering Development
All mechanical and electronic lift components are designed in-house by our experienced engineering team using advanced CAD systems. Cabin interior, control systems, and safety mechanisms are developed with both functionality and aesthetics in mind. Energy efficiency and environmental sustainability principles are also prioritised at this stage.
- Procurement & Production Planning
All components used in the production process are sourced from trusted suppliers with high-quality standards. Once material procurement is completed, our production line is scheduled and optimised to ensure that each part is manufactured on time and without defects.
- Metal Fabrication & Cabin Production
Lift cabins, support structures and guide rails are precisely processed at our facility using state-of-the-art CNC machinery. Laser cutting, bending, welding, and electrostatic powder coating techniques are applied to form durable and aesthetically pleasing components. Cabin interiors can be customised to suit client preferences, including stainless steel, glass, or wood finishes.
- Pre-Assembly of Mechanical Components
Core mechanical components such as the motor unit, counterweight system, door mechanisms and guide rails are prepared for installation at our manufacturing plant. This pre-assembly stage allows for in-house quality checks and significantly streamlines the installation process on-site.
- Integration of Electrical & Automation Systems
The brains behind the lift — including control panels, call buttons, floor indicators, and safety devices — are assembled and integrated by our skilled technical team. All systems are tested and programmed in accordance with current national and international safety standards such as EN 81.
- Quality Control & Testing Phase
Before dispatch, every lift system undergoes thorough quality control and performance testing. Lifting capacity, braking power, electrical connections, and structural integrity are evaluated to prevent any potential issues once installed. These checks ensure a safe and smooth user experience.
- On-Site Installation (With Ametal and Authorised Partners)
At Ametal, we deliver the manufactured lift components directly to the installation site and carry out the installation process either with our own expert teams or in collaboration with authorised installation partners. Depending on the project requirements, the installation and commissioning phases are handled by Ametal or our trusted solution partners. All installation activities are performed in full compliance with local regulations and standards, ensuring the system is handed over to the end user safely and reliably.
- After-Sales Support & Spare Parts
To ensure long-term performance and reliability, we provide continued support through spare parts supply and technical consultation. Periodic maintenance and system checks are performed by certified service providers, ensuring optimal operation throughout the product’s lifecycle.
Conclusion
The lift manufacturing process is not simply about building a machine — it’s about delivering safety, performance, and peace of mind to those who use it every day. At Ametal, we take pride in managing every stage with precision, from engineering design to quality assurance.